With state-of-the-art cutting equipment and a large team of stone experts, we can make virtually anything and get involved with any type of project. We look at how your bespoke stone order is created.
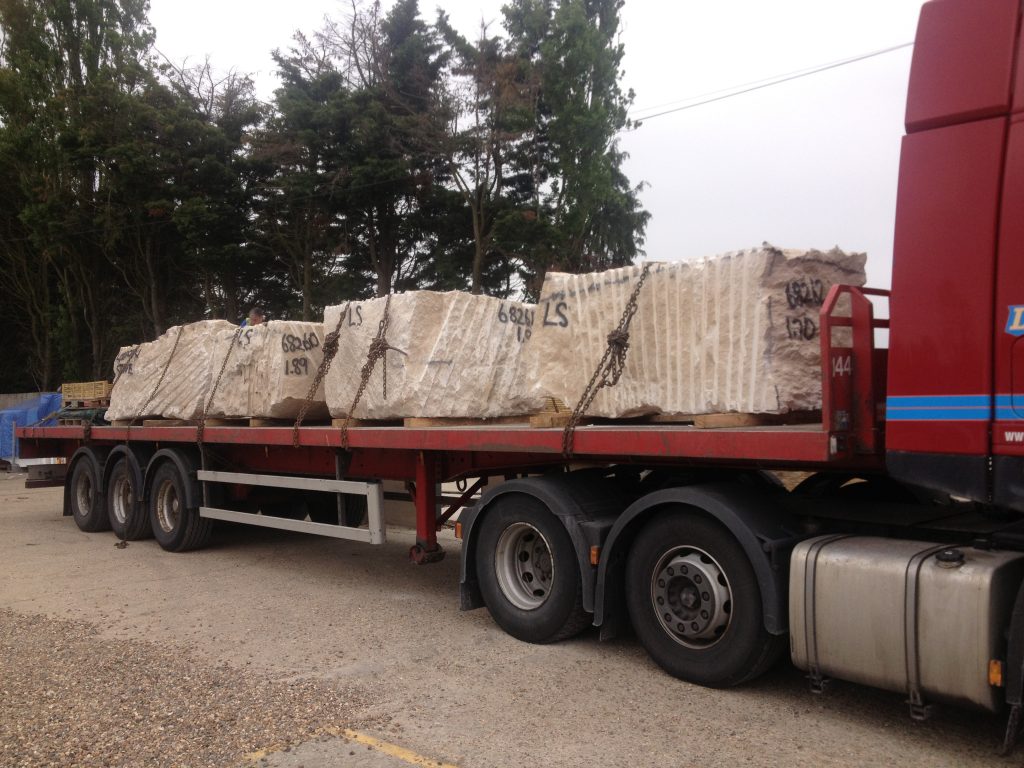
Receiving stone blocks
A large number of bespoke paving orders involve high-end British stone and we regularly take deliveries of blocks of Yorkstone, from quarries near Leeds, and Portland limestone, from the Isle of Portland, Dorset. These can weigh anything from two tonnes up to 14 tonnes.
When we source blocks we always look for the largest available, with a regular shape. This reduces wastage. Small blocks can produce as much as 50% wastage, which goes against the grain—a waste of beautiful stone, environmentally unfriendly, financially unviable.
Creating scants
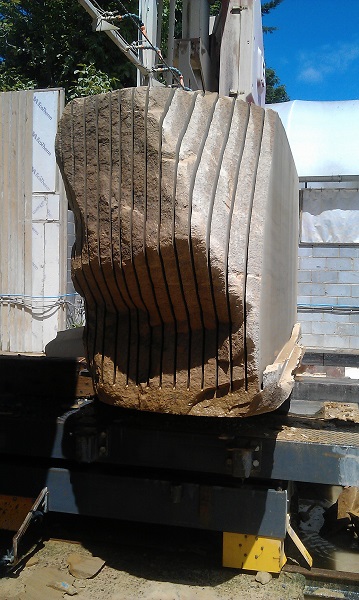
Blocks are moved around the yard using a huge forklift and stored ready to be cut. When required, we then cut these large blocks into rough, unfinished slabs. These slabs are called scant. Large slabs are prised away from the block to be cut down to size.
London Stone used to buy all our Yorkstone and Portland paving as scant, but this created supply issues. In busy times, we were often left without Yorkstone scant for up to 10 weeks.
If you know us, you’ll know this isn’t the London Stone way. We hated not having control over our own lead times—it makes it difficult to give the top-quality service that we always aim for.
The answer was to buy our own block-cutting machinery.
Cutting stone
Cutting a block of stone can take up to 24 hours. This makes choosing large blocks all the more important, as smaller blocks, not only increase the amount of waste, but also increase the machine’s downtime with the pauses needed to change blocks over.
Creating paving from scant
The most common items we produce from scant are paving slabs and step treads, but a high-quality design may also require coping stones, pier caps and swimming-pool surrounds.
To make these, we prise scant away from the main block and cut them down to size. It could be any stone, but Yorkstone, Portland and sawn sandstone are what we most commonly work on.
Cutting machinery used to consist of block saws—diamond-tipped circular saw blades which cut slices off the boulders as if it were a loaf of bread. Nowadays, we use wire saws.
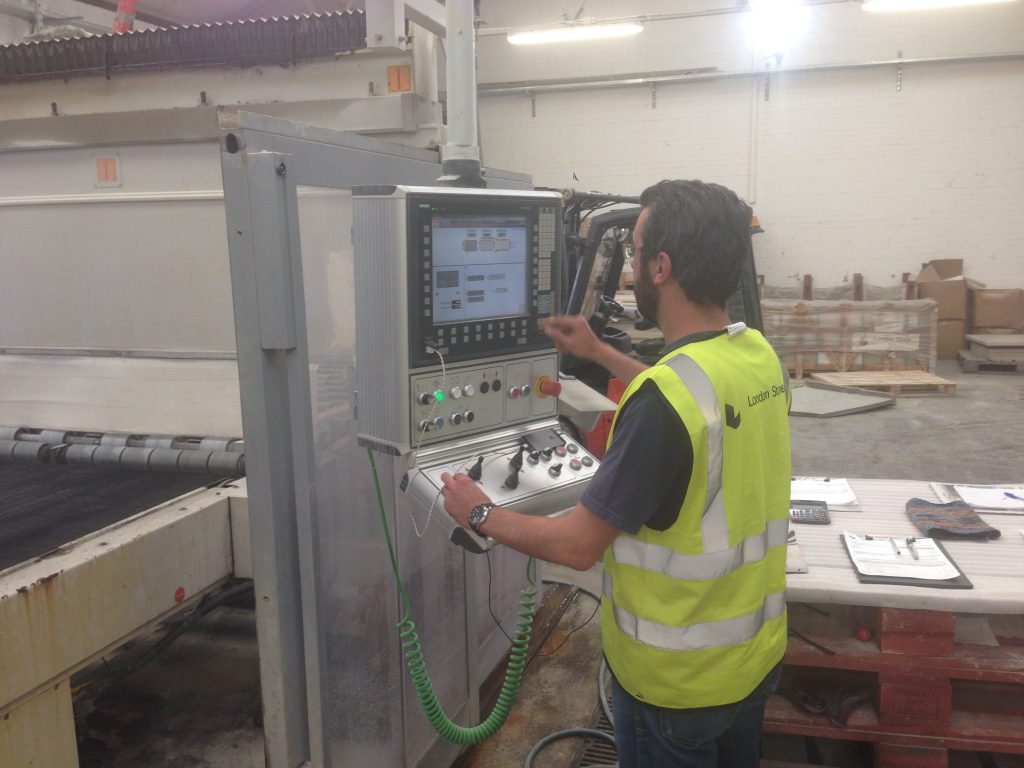
However, we also use CNC machines, which are programmed to produce the exact shape and size required, and are capable of executing very complicated designs in the hands of an experienced operative.
Some stone is cut by a high-pressure water jet. Using water cutting increases flexibility. Circles, for example, are quickly and easily cut from sawn sandstone, and radius coping stones and step treads are much easier to realise. Despite the power, the water jet is gentle with the stone, leaving a very clean and chip-free finish.
Finishing by hand
While the majority of our stone masonry work is done by machines, there are always elements that need to be finished by hand. For example, the majority of a bullnose edge is created by machine, but it still needs to be finished by hand with a sanding pad to get the finish just right.
Every piece of stone that goes through our Bespoke Stone Department has its surface lightly polished. This removes any superficial defects or production marks. It adds to production time, but we refuse to compromise on it, as it provides a superior finished product.
Packing bespoke paving
The final stage is sending the paving on its way. Packaging is every bit as important as all the stages that have gone before. Bespoke and sawn paving needs to be thoroughly packaged, not just because the customer deserves it to arrive in the best condition, but also because, with bespoke paving, it can take weeks on months to make replacements for damaged materials.
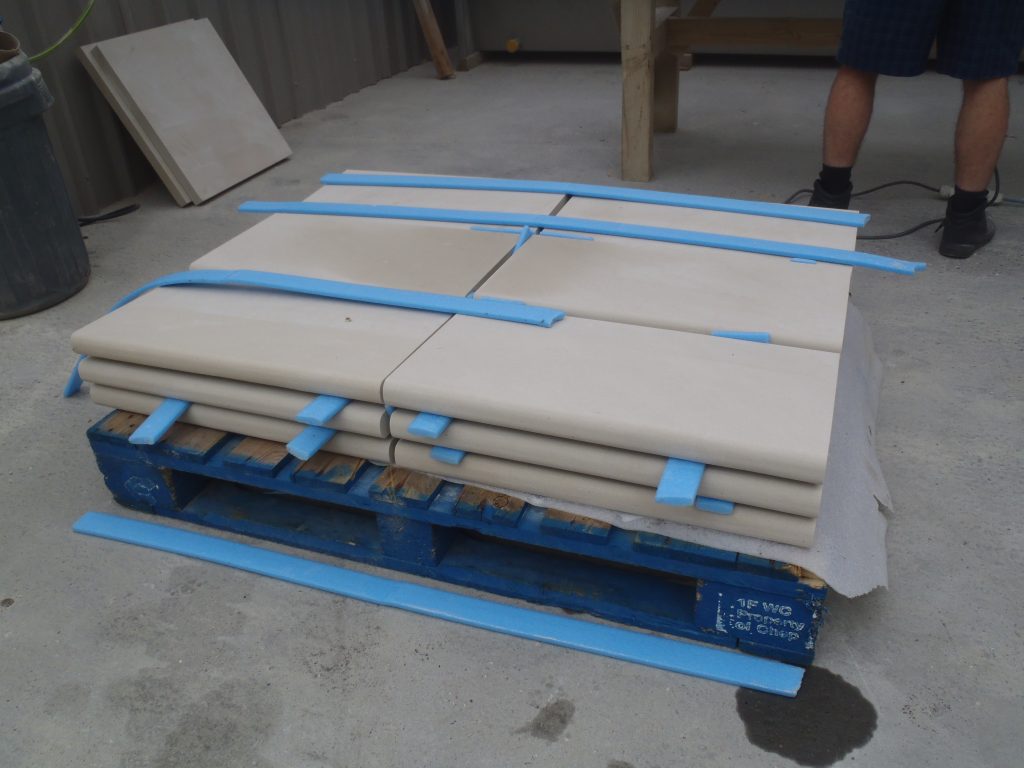
Sawn sandstone and limestone are susceptible to chips because of the way they are cut. When stone is sawn, the edges are very sharp, which means they can be easily damaged. This is why you select an edge profile for step treads, coping and pier caps.
With our paving, we slightly chamfer the edges of our sawn slabs, to reduce the likelihood of chipping.
Sawn paving is packed to ensure that slabs do not rub against each other during transport. When this occurs, it’s one of the most common sources of damage.
Damage from nails protruding from crates is also common. Not only can they damage the stone, but they can leach rust marks onto it. We ensure any exposed nails are removed or covered with thick foam.
About our Bespoke Stone Centre
In 2013, we moved our entire Bespoke Masonry department indoors. This had a major impact on our production abilities. It allowed us to create a production line in a neat and tidy environment—all the more so since we adopted Lean principles to streamline production and workflow.
We have also constantly updated our processes with the latest equipment and machinery which speed and improve production, while working to reduce environmental impact. Two huge improvements implemented soon after we moved, for example, were the addition of a sludge press which removes all the dust from the water so it can be re-used. This saves money on water bills, and is a much more sustainable and environmentally friendly method of production. The quality of the recycled water is so good that we can even use it to operate our jet washes.
At the same time, we installed an edge-profiling machine that could automatically change the profile, instead of it being done by hand; it could also calibrate stone at the same time, resulting in a better quality product that clients found faster and easier to lay.
Watch our video to find out what landscapers and designers think of our bespoke stone service.
How can we help you?
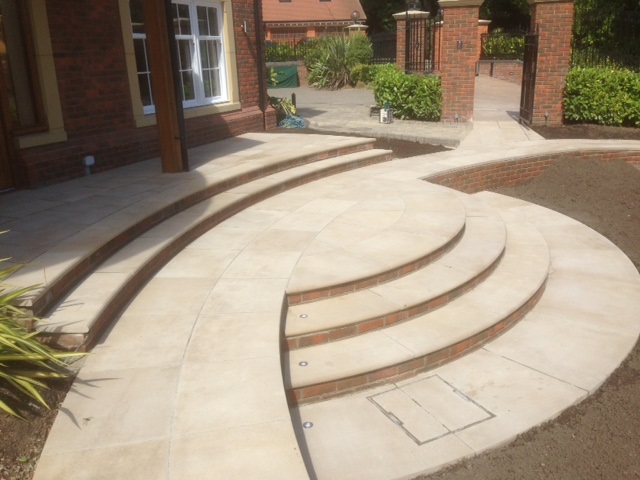
London Stone’s Bespoke Stone Centre is well known in the industry. Our services are particularly popular with designers and architects who look to put their own unique stamp on a project. But bespoke stone is something that anyone can use to make a garden their own. We can also engrave - even porcelain which most people find extremely challenging. Engraving is a lovely way to add a really personal touch in the form of a date, initials or pattern. No job is too small.
The possibilities really are endless and highlight the bespoke capabilities of natural stone and porcelain. The only limit is your imagination. To discuss your bespoke stone requirements, get in touch with our Bespoke Stone Centre today.
Post updated: August 2023