Wondering how porcelain tiles are made? Here's how our Italian suppliers do it. They've been making high-quality porcelain for decades and it’s fair to say that they’ve got it down to a fine art.
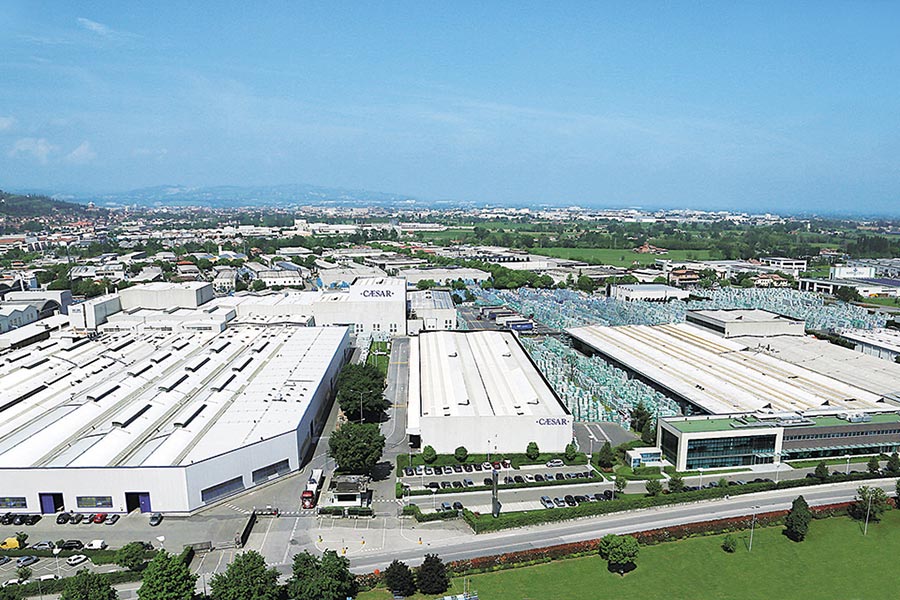
What are porcelain tiles made of?
Porcelain outdoor tiles are made from natural materials: feldspar, kaolin, quartz and clay. In a process lasting 6-8 hours, these materials are mixed together in huge drums. With them are water, colour pigment and an abrasive grinding media about the size of a hockey ball. The balls make the particles in the raw materials into a uniform spherical size. This is very important later on when the material is vitrified.
Once the mixing process is complete the water (and the balls) are extracted and the remaining semi-wet material is pressed to the correct thickness.
Different styles and textures
Different-styled presses are used to create the required surface textures. Our Italian suppliers are continually adding new finishes and size formats and the stone- and wood-effect tiles are extremely realistic. Every porcelain style includes up to 20 individual tiles with different surface patterns. This means repeated tiles are less obvious and the finished installation takes on its own unique character.
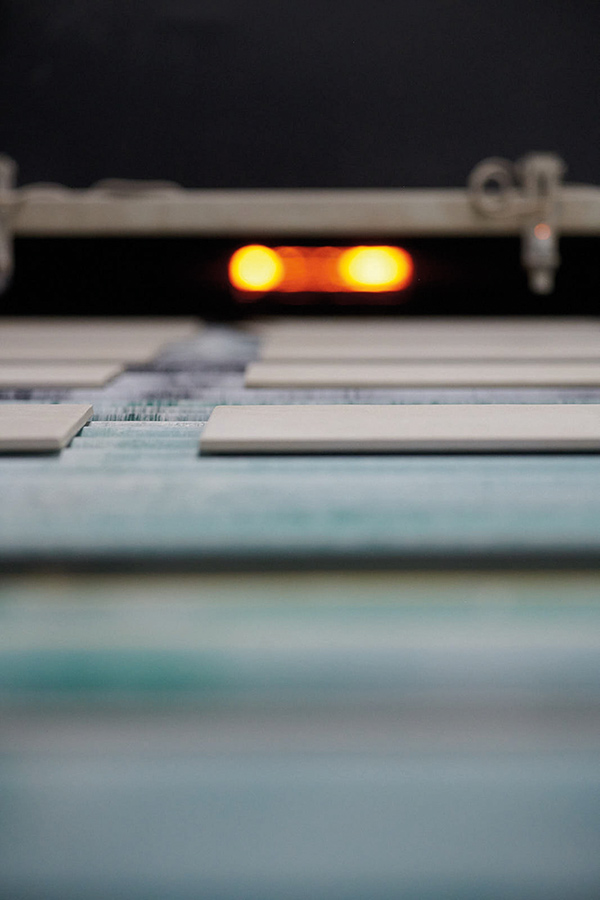
The advantages of Italian manufacture
When we looked at other manufacturing methods, the difference was immediately obvious. The Italian product is full-bodied—the colour penetrates the whole way through the tile, thanks to that addition of pigment in the mixing process.
On lower quality products the colour is printed on the surface only, so the body of the paver is a different colour. This means that when the edge of a tile is profiled - as a step tread or coping - the two-tone manufacture is visible.
Fired to a very high temperature
The pressed porcelain is baked in a kiln, initially at a temperature of 300°C. The heat then rises to 1240°C before coming back down to 300°C. Firing takes about four hours. This is where the even, spherical size and shape of particles and a consistent mix is so important. When fired correctly, these materials fuse uniformly and create an incredibly dense structure, giving porosity values of 0.05%.
Why particle size is so important
If natural materials are not prepared to the same level, the quality won't be the same. Where manufacturers can't or don't meet these standards you're often left with a higher porosity of up to 0.5%—meeting the ISO standard but not giving clients the required high stain-resistance and low maintenance.
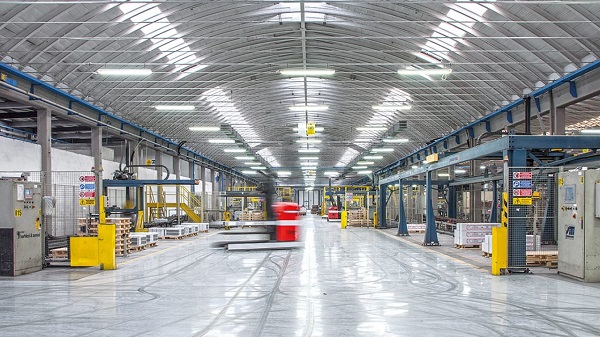
Dried on racks
After firing, the material is stored on huge five-metre high racks to cure. The racks are loaded automatically by a conveyor belt. When they are full, robots swiftly take them away and replace them with empty ones ready to load.
Cut to size
Then comes the most interesting part of the whole process: rectification. One of the most attractive features of porcelain outdoor tiles is their fully rectified dimensions. Unlike natural stone slabs, these tiles offer no tolerance - each one has exactly the same dimensions. How is this done?
Once the product is cured, finished dimensions can be anything from 6-8mm over size. The pressed, fired porcelain is now moved along a conveyor belt, through milling heads that remove a fraction of material from each edge. By the time the product reaches the end of the milling conveyor line, each tile measures exactly the same.
In the wet!
Sounds like a normal conveyor belt? It is, but for one small difference—it's under water. When working with a material as hard as porcelain, using a submerged milling process ensures optimum performance of the milling tools, not to mention offering the ultimate form of dust suppression. That’s why the edge of the porcelain tiles is so smooth—because it’s been milled under water.
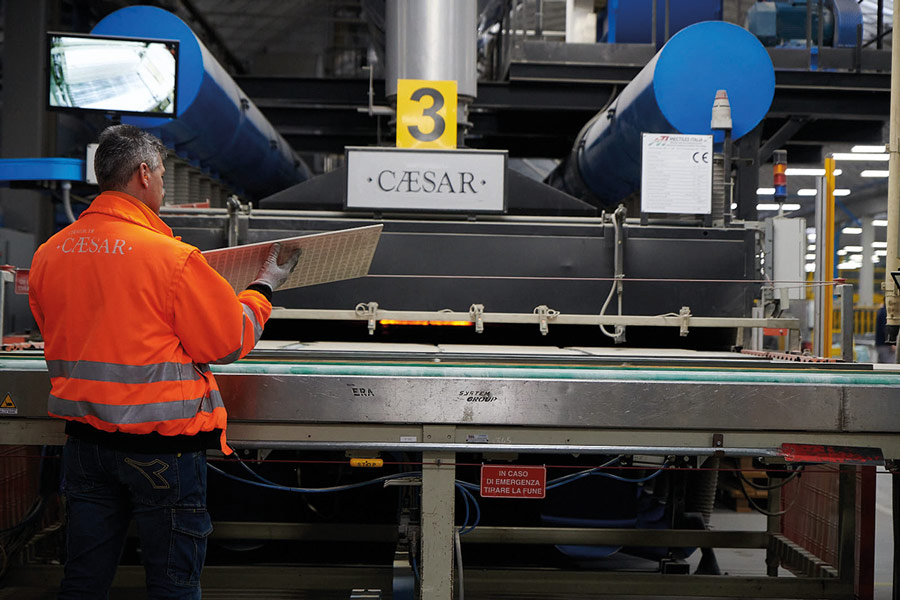
Scanned for quality
High-tech production solutions continue as we roll into Quality Control. Every single slab of porcelain goes through a scanner and is, effectively, X-rayed. The X-ray picks up cracks, fissures and any production defects, while also carefully monitoring surface texture and colour. Anything less than perfect simply doesn’t make the grade.
Our porcelain guarantee
So, you can see the massive investment that goes into a high-end porcelain factory. This efficient, consistent automation is a huge entry barrier for most companies and explains why some products fall short of the quality mark. The manufacturing environment needs to be clean, fully resourced and highly automated.
We chose our Italian porcelain manufacturer for their top-quality processes and outstanding products. We're so confident of the quality of the porcelain tiles we supply that we offer a 10-Year Guarantee.
View our complete porcelain range now.
Updated: November 2022