In October 2010, London Stone’s Managing Director Steve Walley made a trip to Kota, Rajasthan, to visit the company’s suppliers and discovered how things were changing in Indian sandstone production. This is the account he wrote at the time.
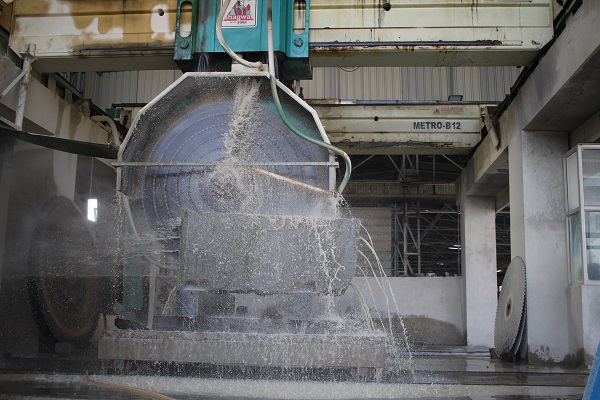
The road from Jaipur to Kota is narrow. We’d set off late and it was dark. Dogs, cows, motorbikes and cars crowded the pot-hole strewn route, all contending with the constant procession of trucks streaming between the two cities. Everybody drives on full beam, with no exceptions, and the result is that you’re completely blinded for most of the drive. It wasn’t uncommon to round a blind bend to be faced with a truck on your side of the road, trying to overtake another. Cows sprang from nowhere and the driver constantly had to brake sharply, making last-ditch manoeuvres to avoid hitting this, India’s most revered resident.
I have never been so pleased in my life to reach the sanctuary of bumper to bumper traffic, and the relief of crawling the last few kilometres into Kota.
Kota, centre of the sandstone industry
Kota is the heart, lungs and backbone of Indian sandstone industry and I was here to visit the seven stockyards owned by our newest supplier. Near the town centre, its stone market consists of a conglomeration of everything from the tiniest enterprise, making bits and pieces of the domestic market, to the enormous stone-shipper’s site. Crowded together in every direction for two miles and more, the concentration of producers in this area is phenomenal.
Large trucks roll down rabbit-lane lanes with massive blocks of sandstone from nearby quarries. Smaller lorries arrive packed with layer upon layer of sandstone to be hand-dressed and packaged. If motorised transport is unavailable—or unattainable—there is always the trusty camel.
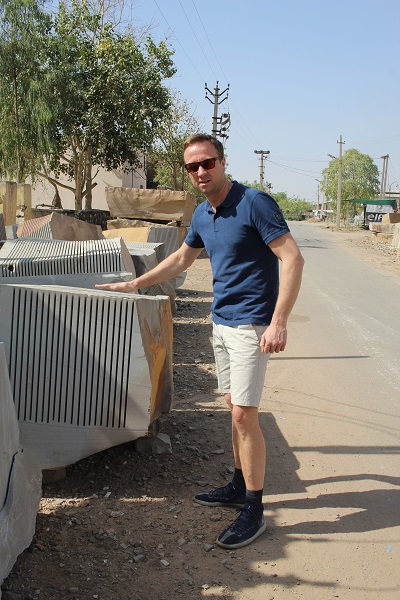
Sandstone production
First stop, our supplier’s factory where the majority of his calibration is carried out. Over the past couple of years, paving calibration has become more widespread and offers cost-savings to manufacturers, importers and installers. Neat stacks of freshly calibrated Kota sandstone awaited packaging; mountains of sandstone block pavers were piled up, waiting for the overworked calibration machine.
The quality of the finished Indian sandstone paving was as good as anything I’ve seen, thanks to rigorous quality control. Every crate is numbered and signed off, so any quality issues can easily be traced back to an individual. The result is that the staff are extremely thorough. Any material not up to standard is set aside for the local market or sent back to the stone masons for further dressing.
Payment of workers
There is a common misconception that the labour used to produced Indian sandstone paving is cheap. This is not the case. There is a huge worldwide demand for Indian natural stone and the demand is so great that there is actually a shortage of skilled stone masons. This means that experienced masons can demand a high price for their labour and are, by Indian standards, very well paid.
Onsite packaging production
Next stop, a small unit which constructs crates. This particular supplier makes crates from scratch. A saw mill never-endingly chops logs into timber struts and bearers. All waste timber is bagged up and sold for firewood. A constant stream of people queued up at the antique scales which weighed the firewood bags. Nothing was wasted.
Budhpura – centre of controversy
The cobble-making village of Budhpura, our final stop of the day, has been the subject of intense media attention for the last two to three years, due to the high levels of child labour. I first visited five years ago in 2005 and witnessed the disturbing sight of children as young as five producing sandstone cobbles. We take our responsibility for sourcing ethical sandstone very seriously and I was keen to see if there had been any effect on the ground.
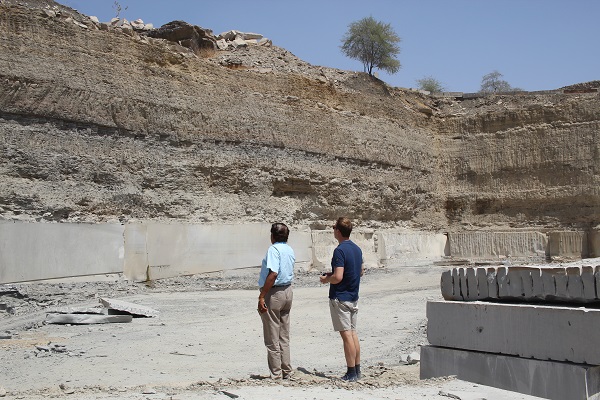
Ethical trading
Budhpura has a long street with small independent cobble producers on both sides. London Stone is committed to ethically sourced sandstone and, as a member of the ETI (Ethical Trading Initiative)*, we are required to visit to fulfil our trading objectives. Our supplier proved to have a clean, organised, productive yard with a mix of men and woman aged from 16 to 60 carrying out the work.
My final morning in Kota included a six-course Indian breakfast. I was still full after being taken out by my supplier the night before. A big mistake you can make here is to finish your plate of food off, because it will be instantly replenished before you can raise an objection. One thing you can always be sure of in India is amazing hospitality
The future of Indian sandstone production
The overriding feeling I have is of the speed of progress taking place in India. When I first travelled there five years ago in 2005, there was no highway to the quarries and the trip there was a nightmare. Kota is developing fast, with Walmart and McDonald’s a sure sign of Western influence.
Perhaps the best indication of progress in sandstone production, though, is mechanisation and the adoption of health and safety measures. A visit to one of the stone producers found three new machines for tumbling paving. Seventy-five per cent of the workers were wearing hi-vis clothing, and 50% wore safety boots. When I asked why not all of the men were wearing boots, he said it takes a bit of time to change staff habits; some have been stone masons for 20 years and the idea of wearing PPE is alien to them. Most of the younger staff were in PPE.
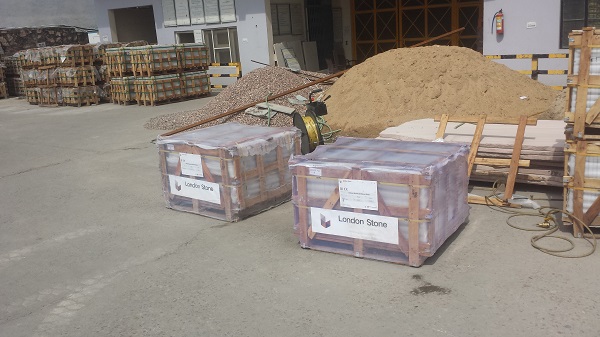
Modernisation in the Indian sandstone industry
Another visit was to “the old man”, an engineer who runs a small factory in Jaipur, churning out very high-quality products in an efficient and extremely productive operation. He was in the midst of modernising his plant with two state-of-the-art water processing machines. I was amazed. The “water blaster” was, in essence, an extremely powerful jet wash, which gave a honed piece of Sagar Black a shot-blasted texture and appearance within about sixty seconds.
The ”water cutter”—familiar to us—is considered to be innovative for a small Indian paving producer. CNC-controlled, it can cut to a depth of 100mm and be left to do its job according to the CAD drawings programmed into it.
Mechanisation is moving forward at pace. It’s a sad fact that smaller, independent companies will gradually be squeezed out of the market, but mechanisation also represents progress in terms of reduction of child labour, greater health and safety standards and, by de-skilling the work, opens up this massive industry to people without stone mason skills.
One thing that hasn’t changed, and probably never will, is the power of India’s cows. Answerable to no one, they do what they want. It’s not uncommon to see half a dozen strolling brazenly down the wrong side of a highway or asleep in the fast lane. If a cow is crossing the road, you’d better be sharp on your brakes or quick on the steering wheel because, one thing is certain, however fast we move forward, the cow will go at its own pace.
*London Stone is no longer a member of the ETI but is very much involved in a scheme to end child labour and improve working conditions for men and women in the Budhpura area. Read more on our approach to sourcing Indian sandstone.
Post updated: June 2024